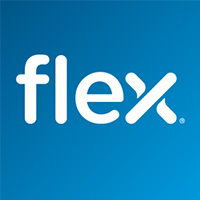
Description
Flex is the diversified manufacturing partner of choice that helps market-leading brands design, build and deliver innovative products that improve the world.
We believe in the power of diversity and inclusion and cultivate a workplace culture of belonging that views uniqueness as a competitive edge and builds a community that enables our people to push the limits of innovation to make great products that create value and improve people's lives.
A career at Flex offers the opportunity to make a difference and invest in your growth in a respectful, inclusive, and collaborative environment. If you are excited about a role but don't meet every bullet point, we encourage you to apply and join us to create the extraordinary.
Job SummaryPrinciple Accountabilities:
- Develops, maintains and improves all test and burn-in processes within area of responsibility.
- Periodically reviews all process specifications to determine if it accurately reflect the process requirements and test techniques. Updates the specifications as required.
- Ensures that test and burn-in processes are within all safety specifications.
- Consistently reviews quality yields and develops corrective actions to eliminate any yield detractors, further improves the process reliability.
- Assists with the fabrication and development of new equipment, fixtures and test programs (where applicable).
- Ensures that effective preventive maintenance, diagnostics, and daily measurement schedules are in place for each test and burn-in process.
- Coordinates preventive maintenance activities. Ensures that scheduled preventive maintenance activities are completed according to the specified schedule.
- Assists engineering and the development labs with all new product introduction and development.
- Coordinates and monitors all FIMPA or product off-load activities for assigned test and burn-in processes.
- Ensures that each test and burn-in process has a training/certification package for both manufacturing and maintenance. Facilitates the completion of these training/certification packages with the appropriate engineer(s) and the Resource Development Department.
- Partners with Industrial Engineering on all equipment moves or line re-arrangements as required.
- Drives recovery actions/repair of any test or burn-in process that is down. Coordinates recovery/repair activities with the respective maintenance, technicians, engineers, suppliers or maintenance spare parts analyzers whose area of competence is necessary to get the process back in working order.
- Assists test engineers in development of disaster recovery plans for each test and burn-in process within the area of responsibility.
- Follows Engineering test processes.
- Ability to perform high-level repair, format and "build" software per unit configuration and connect hardware (cables) between multiple units.
- Configures/flashes firmware on Sub-assemblies and connects Ethernet connections between unit(s).
- Understands the basics of Disk Arrays and set up for Disk Arrays.
- Troubleshoots/debugs at multiple system levels. Ability to determine workmanship errors and drive back through quality.
- Performs module verification.
- Be able to troubleshoot wiring of units using schematic diagram and assembly process.
- First line support for workstation and line issues.
- Log and fail defects of units and parts that are defective and address trending failures.
Education / Experience
Typically requires a minimum of an Associates degree, military technical training or equivalent experience and training. Typically requires a minimum of 6 years of related experience.
Knowledge / Skills / Abilities
Demonstrates advanced technical skills which may be used to conduct on-the-job training and/or lead/guide other employees. Highly skilled with ability to move between shifts/ product lines. Demonstrates broad knowledge of functional techniques and has input to process improvement. Has awareness of and may apply new technologies. Ability to read complicated drawings, mathematics, handbook formulas and a variety of testing and measuring instruments. Must have an understanding of manufacturing functions and the ability to train others.
Serves as an expert/consultant in technical skills with other employees. Demonstrates knowledge of advanced technologies as well as functional techniques and improves processes. Applies new technologies and technological changes.
Able to read, comprehend and interpret complex instructions. Ability to effectively present information in one-on-one and small group situations to other employees, leads, manufacturing support and supervisors of the organization.
Ability to define problems, collect data, establish facts and draw valid conclusions. Ability to interpret an extensive variety of technical instructions in mathematical or diagram form and deal with several abstract and concrete variables.
Decision Making / Discretion
Determines quality/testing methods/ procedures on new assignments.
Supervision / Leadership
May edit work or advise other employees. Requires little to no instruction. Requires little to no supervision.
Work Environment:
While performing the duties of this job, the employee is frequently exposed to work that requires repetitive motion. The noise level in the work environment is usually moderate.
Physical Demands: Reasonable accommodations may be made to enable individuals with disabilities to perform the essential functions.
While performing the duties of this job, the employee is frequently required to sit, handle small components, and talk and hear. The employee is occasionally required to stand and walk. The employee must occasionally lift and/or move up to 25 pounds with the aid of a handcart. Specific vision abilities required by this job include close vision, color vision, depth perception, and ability to adjust focus.
Job Category Production EngineeringRequired Skills:
Optional Skills:
Flex is an Equal Opportunity Employer and employment selection decisions are based on merit, qualifications, and abilities. We celebrate diversity and do not discriminate based on: age, race, religion, color, sex, national origin, marital status, sexual orientation, gender identity, veteran status, disability, pregnancy status, or any other status protected by law. We're happy to provide reasonable accommodations to those with a disability for assistance in the application process. Please email accessibility@flex.com and we'll discuss your specific situation and next steps (NOTE: this email does not accept or consider resumes or applications. This is only for disability assistance. To be considered for a position at Flex, you must complete the application process first).
Apply on company website