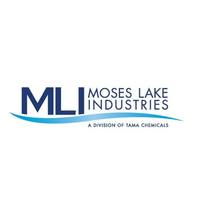
Description
We value: Safety, Integrity, Ownership, Collaboration, Service, Sustainability
Moses Lake Industries, Inc. (MLI) is a rapidly growing producer of ultra-pure chemical products, serving the semiconductor and flat-panel screen industries worldwide. We deliver world class products to the leaders of the industries we serve.
You will be working for a midsized company with great people and a history of steady growth and profitability. Sound like a match? If you are prepared to work in an exciting and rewarding environment, we look forward to considering your experience and qualifications.
Schedule: Monday-Friday, 8am-5 pm, Onsite, Moses Lake, WA
WHAT YOU WILL BE WORKING ON
- Monitor safety standards under all applicable Local, State, and Federal regulations, including (OSHA, and WISHA).
- Provide and conduct training through safety materials, coaching, and mentoring.
- Inspect tools, machines, and equipment for accident prevention, including safety devices and procedures.
- Assist with testing and servicing safety equipment including gas monitoring equipment.
- Observe workers and evaluate job activities to determine the use of prescribed safety equipment such as glasses, hardhats, goggles, respirators, clothing, and other equipment.
- Perform Job Safety Analysis (JSAs) as required.
- Inspect specified areas for fire prevention equipment and other safety and first aid supplies.
- Investigate causes of accidents to identify preventative safety measures for incorporation into the safety program.
- Assist with maintaining programs and record-keeping systems that track and evaluate personnel injuries.
- Perform security program support and access control duties as needed.
- Assist with ISO audits, accident investigations, and site inspections of operational procedures, facility design, equipment, and materials.
- Perform associated functions as an active member of EHSSSC and MLI Safety Committee
- Reviews safety metrics and assists in recommendations based on data.
- Other duties as assigned.
QUALIFICATIONS
- A.S. or B.S. degree in Safety, Industrial Hygiene, applied sciences, or equivalent is a requirement. Safety or related industrial experience may be taken into consideration in lieu of educational experience.
- 1-5 years of safety or equivalent experience.
- EMS software experience preferred.
- Working knowledge of computers and MS Office software.
- Working knowledge of arithmetic and grammar.
- Demonstrated ability to:
- Follow written and verbal instructions in English.
- Manage multiple priorities and projects simultaneously in order to meet established deadlines.
- Work as a team and/or independently.
- Perform tasks with attention to detail and accuracy.
- Maintain regular and punctual attendance
SALARY & BENEFITS
Please note that the salary information shown below is a general guideline only. Salaries are based upon candidate experience and qualifications, as well as market and business considerations.
Summary pay range: $66K-$80K
- Generous PTO: Your off time is important.
- Medical/Dental/Vision: Majority of premiums paid by MLI. Includes virtual medical and mental health options.
- Additional Health Coverage: FSA and HSA available. Voluntary insurance options include life and AD&D, accident, hospitalization, and critical illness.
- Earn More: We offer a generous discretionary bonus program in addition to salary/wage.
- 401(k) Savings Plan: Jump start your retirement with MLI's employer matching contributions.
- Company-Paid Benefits: Long-Term Disability Insurance, EAP, Fitness Club Membership Program, & Education Assistance Program. Relocation Assistance available.
- Additional Benefits: We provide position-based clothing, travel expenses, training and additional materials needed on a case-by-case basis.
WORKING CONDITIONS
Duties are generally performed indoors in an office and high-purity manufacturing environment. The noise level in the work environment is usually quiet to moderate. When working in the presence of safety hazards, the employee is expected to follow company safety rules and use proper personal protective equipment such as hardhat, safety glasses, and full leather shoes, etc. Employees will work in a covered Process Safety Management (PSM) environment containing threshold quantities of flammable liquids and/or gasses that have a potential for fire or explosion. Employees working in this environment are required to be free from devices that are not considered intrinsically safe. Examples of devices that may not be intrinsically safe include Insulin Pumps, Pacemakers, Pain Management devices, etc.
Apply on company website