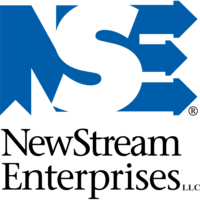
Description
Monday-Friday 7:00am-3:30pm
POSITION SUMMARY:
Reporting to the Engineering & Quality Manager, the Quality Technician is responsible for assessing product and evaluating processes to ensure compliance with customer requirements. The role assists with QMS required documentation, testing procedures, and error-proofing. The Quality Technician is also responsible for assisting operators in correcting non-conformances and providing training and feedback resulting from product assessment and customer complaints utilizing Lean Manufacturing principles and problem-solving techniques. The role supports and participates in incoming and outgoing boom lift inspections.
ESSENTIAL DUTIES AND RESPONSIBILITIES:
- Perform product audits and inspections on manufactured or assembled products to assess conformity with specifications by evaluating dimensional, visual, and other results as defined in process instructions. Discuss audit and inspection results with those responsible for products and recommend necessary corrective actions.
- Observe and monitor production operations and equipment to ensure conformance to specifications and recommend necessary process adjustments.
- Assist in activities associated with response to nonconforming product, such as parts quarantine, evaluation and assessment of inventory, root cause analysis, and solution implementation.
- Provide training on production methods and other topics as needed in response to nonconforming products, customer complaints, and preventive and corrective action.
- Manage all aspects of gauging and torque tools, including ordering, tracking, calibration schedule, retiring gauges, and recording and maintaining gauge calibration data.
- Perform and document gauge verification activities. Performs minor repairs on gages as needed. Ensures that malfunctioning and/or out-of-calibration gages and tooling are quarantined to prevent use.
- Provide training as needed to ensure proper use of gauges and torque tools.
- Operate boom lifts, primarily during testing and process development.
MINIMUM QUALIFICATIONS PREFERRED:
- High school diploma or equivalent combination of education and experience
- Five years of experience in a production facility, preferably in a manufacturing or remanufacturing environment
- Familiarity with product testing methods, quality control, and LEAN manufacturing practices
- Ability to use gauges required for product audit and inspection
- Good interpersonal skills and ability to explain technical concepts
- Good oral and written communication skills to effectively communicate with internal and external customers
- Good time management and organizational skills
- Good computer skills, especially in MS Excel, MS Word, and MS Outlook
PREFERRED SKILL/ KNOWLEDGE/ ABILITY/ EDUCATION/ EXPERIENCE:
- Degree, or continuing education pursuing degree in Mechanical/Electrical/Industrial Engineering or a related field
- Quality auditor certification (CQA)
- Strong knowledge of manufacturing processes and procedures
- Experience with ERP systems (specifically Infor CSI) and project management software
- Knowledge of Quality Management Systems (QMS), ISO standards, and environmental regulations
- Internal Auditor Training
GENERAL RESPONSIBILITIES:
- Ensure QMS (Quality Management System) guidelines and regulations are followed
- All employees are required to follow and promote all company and regulatory safety and environmental standards and exhibit safe work practices at all times
- Use of PPE (Personal Protective Equipment): Safety Toe Shoes, Safety Glasses, etc. required in production and warehouse environments
- Follow established departmental policies, procedures, objectives, and continuous improvement objectives
- Actively participate in and support the principles of Open-Book Management
- Exhibit a positive attitude and promote a positive work environment
WORK ENVIRONMENT:
Work is performed partially in a controlled atmosphere. Some exposure to harsh conditions for long periods of time is possible. This employee will be required to demonstrate continued knowledge of Haz/Com regulations and requirements. All employees are required to follow safety standards and wear all personal protective equipment in designated areas.
PHYSICAL DEMANDS:
Sitting 25%, Standing/walking 75%. The ability to lift and carry up to 50 pounds is required. The physical demands described here are representative of those that must be met by an employee to successfully perform the essential function of this job. While performing the duties of this position, the employee is regularly required to walk, stand, stoop, kneel, crouch, use hands and fingers to handle or feel, and reach with hands and arms climb or balance.
Apply on company website