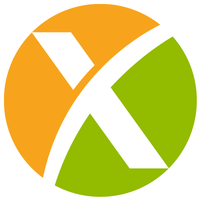
Description
Job Description:
The Assistant Manager - Manufacturing Process (Mechanical) position will be based in Hyderabad, India. In this position, you will report to the Power Electronics Sourcing Director. We are seeking a talented Manufacturing Process Engineer to play a critical role in optimizing our production processes. In this role, you will leverage your expertise in Lean Six Sigma methodologies to partner with internal and external stakeholders, ensuring a smooth transition of new electronic products from development to high-volume production. You will work collaboratively across various departments, including engineering, sourcing, and quality, and program management to analyze existing processes, identify areas for improvement, and implement data-driven solutions that enhance efficiency, yield, and overall product quality. Watch this video to learn why Nextracker is more than just a place to work.
We are looking for someone who demonstrates:
- Passionate drive to innovate and create
- Integrity to the core
- Enthusiastic customer focus
- Consistent interactive teamwork
- Desire for continuous improvement and top performance.
Here is a glimpse of what you will do:
- Collaborate with R&D teams to manage transfer from prototype to mass production. Partner with external suppliers to document and analyse manufacturing processes for mechanical and motion control products.
- Identify and implement critical to quality (CTQ) characteristics and create control plans to ensure product quality and consistency, utilizing tools like Failure Mode and Effects Analysis (FMEA) and Process Flow Mapping (PFMEA) to define potential failure modes and their impact on CTQs.
- Analyse production data to evaluate yield, capacity, and identify opportunities for process improvement. Leverage statistical process control (SPC) techniques like control charts (e.g., X-bar R charts, c-charts) to identify process variation and opportunities for improvement.
- Implement Lean Six Sigma methodologies to optimize manufacturing processes, reduce waste, and improve efficiency. This may involve techniques like:
- Value Stream Mapping (VSM) to identify and eliminate waste in production processes.
- Kanban systems to improve material flow and manage inventory levels.
- Poka-Yoke (mistake-proofing) methods to prevent defects from occurring.
- Design of Experiments (DOE) to optimize process parameters and reduce variation.
- Develop and maintain process documentation, including work instructions and control plans, ensuring they are clear and concise.
- Conduct process audits to identify areas for non-conformance and recommend corrective actions based on Lean Six Sigma principles.
- Work collaboratively with engineering teams to identify and implement process improvements based on data analysis and statistical processes.
- Manage and track projects related to process optimization adhering to DMAIC (Define, Measure, Analyse, Improve, Control) methodology.
Here is some of what you will need (required):
- Bachelor's Degree in Engineering, Manufacturing, or a related field.
- Minimum 10 years of experience in a manufacturing process engineering role, preferably within the solar, industrial motion control, automotive or commercial building products industries.
- Experience in working at supplier locations and working collaboratively with external teams.
- Experience working in a contract manufacturing environment preferred.
- Proven expertise in Lean Six Sigma methodologies (Green Belt or Black Belt preferred).
- Strong understanding of statistical process control (SPC) techniques, with experience applying control charts to analyze process data.
- Flexible to travel.
Here are a few of our preferred experiences
- Excellent analytical and problem-solving skills, with a data-driven approach to process improvement.
- Strong communication, collaboration, and interpersonal skills.
- Ability to manage multiple projects simultaneously and meet deadlines.
At Nextracker, we are leading in the energy transition, providing the most comprehensive portfolio of intelligent solar tracker and software solutions for solar power plants, as well as strategic services to capture the full value of solar power plants for our customers. Our talented worldwide teams are transforming PV plant performance every day with smart technology, data monitoring and analysis services.
For us at Nextracker, sustainability is not just a word. It's a core part of our business, values and our operations. Our sustainability efforts are based on five cornerstones: People, Community, Environment, Innovation, and Integrity. We are creative, collaborative and passionate problem-solvers from diverse backgrounds, driven by our shared mission to provide smart solar and software solutions for our customers and to mitigate climate change for future generations.
Culture is our PassionApply on company website